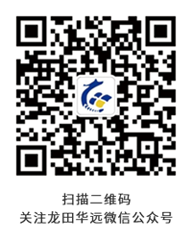
系统演示
掘进机惯导纠偏系统
RINR(Roadheader Inertial Navigation Rectification System)
系统描述
系统在原有设备上加装激光雷达、高精度惯导等传感器对掘进机的姿态和行程进行监测。利用基于RoS平台的SLAM算法等无人驾驶技术,实现掘进机的定姿、定位,并与掘进机控制系统联动,具备定姿、中线自动校准等功能。系统实时解算出实际的掘进曲线并实时指导纠偏。可广泛应用于掘进机、掘锚机、连采机等掘进场景。
现场痛点
1.全站仪+惯导的掘进机定位方式,每掘进100米,需要重新设置全站仪标靶位置,进行移靶,费时费力
2.井下环境煤尘、粉尘浓度高,严重影响全站仪测量精度,掘进时全站仪还存在脱靶问题
3.掘进机定位不准,无法实现掘进的自动化、智能化、快速截割
4.作业空间局限,导致视野受限,无法全面观察煤墙及设备整体运行情况,影响对设备的调节
解决方案一:在掘进机上安装激光雷达+倾角传感器,利用RoS+SLAM算法对掘进机进行定姿定位
解决方案二:在煤壁顶端安装激光雷达,在掘进机上安装高精度惯导,利用STD目标识别算法,激光雷达多点检测掘进机相对位移,实现定姿定位
对比传统全站仪+高精度惯导的方案,具有如下优点
| 全站仪+惯导方案 | 方案一 | 方案二 |
算法 | 算法最简单 | 算法较复杂 | 算法最复杂 |
价格 | 价格最贵 | 价格约为全站仪方案的20% | 价格约为全站仪方案的60% |
基站移动 | 约百米移动一次 | 无需移动 | 约百米移动一次 |
是否校正标靶 | 需要 | 不需要 | 不需要 |
粉尘影响 | 非常大 | 较大 | 最小 |
适用范围 | 友商采用最多 | 煤巷掘进,快速掘进 | 普通巷道掘进,每百米移动雷达一次 |
系统功能
1.利用人工智能算法对安装在掘进机机身的惯导姿态监测信息进行修正,实时检测掘进机三维空间位置及姿态,具备井下掘进机自主导航功能和井下掘进机坡度追踪功能
2.系统实现了掘进机行走精确定位,行程误差低于千分之一
3.系统实现了掘进机井下精准定姿,航向精度≤0.1°,水平两轴姿态精度≤0.03°
4.系统具备掘进机自动纠偏功能,通过对掘进曲线的监测,当掘进中线发生偏移时,可进行一键自动校准
5.上位机中对传感器原始数据实现数字化分类与存储;可按班次、日、周、月输出掘进相关数据及其对应绘制的掘进巷道曲线和偏移差值等信息
6.可根据掘进机型号进行定制化开发,普适性强,经济效益更高
7.系统预留RS485、RJ45等通讯接口,采用标准Modbus TCP协议,并免费开放数据接口
8.系统可联网,支持远程数据查询和控制
系统特点
1.系统采用基于RoS平台的SLAM算法,不受传感器自身精度的限制,可达到更高的定位精度,且多线激光雷达的造价相较于全站仪的造价更便宜
2.可实时监测,无需人工测量,不受粉尘、标靶移动的影响,节省检测时间、保证掘进工期
方案一
1.煤矿地质条件较好时可将多线激光雷达安装在掘进机机身上,无需移动基站、激光雷达等,适用于煤巷掘进
2.系统可有效解决全站仪脱靶问题,且激光雷达抗污损能力强于棱镜,提高了掘进速度
3.对比传统全站仪+高精度惯导方案,成本降低约80%
方案二
1.通过将激光雷达吊装在掘进机后的巷道中,不受掘进时工作面煤尘、粉尘的影响,不会影响激光雷达的测量精度
2.系统采用的多线激光雷达有多个激光发射组件,可同时发射多束激光,利用STD识别算法,识别有效激光束,不受巷道起伏的影响,不会发生脱靶情况
3.对比传统全站仪+高精度惯导方案,成本降低约40%